KingsBox supply chain is the network of organizations, people, activities, information, and resources involved in the creation and delivery of a product. It includes all the activities involved in sourcing materials, manufacturing and assembly, warehousing and distribution, and the delivery of the final product to customers.
The supply chain starts with the sourcing of materials, then the process of turning those materials into a finished product, and finally delivering that product to the customer. Along the way, there are many different players involved, such as suppliers, manufacturers, distributors, logistics providers, and retailers.
Effective supply chain management involves coordinating and integrating these activities to minimize costs and optimize the overall performance of the supply chain. This includes activities such as forecasting demand, managing inventory, and logistics planning, as well as managing relationships with suppliers.
In recent years, supply chain management has become increasingly important as the KingsBox department. Also, global competition has intensified and the pace of business has accelerated. We are always under pressure to deliver products faster, cheaper, and with better quality, which requires efficient and effective supply chain management.
Let’s take a look at how we organize the supply chain at KingsBox, to receive all the equipment in time and successfully deliver it to our clients.
Indice dei contenuti
Three branches of the KingsBox supply chain
Purchase department – team that purchases the right products
The purchase department, also known as the procurement department, is a functional area within a company that is responsible for acquiring goods and services needed for the organization’s operations. The primary role of the purchasing department is to purchase the right products, at the right time, in the right quantity, and at the right price.
The KingsBox purchase department is responsible for a variety of tasks, including:
- Identifying the company’s purchasing needs
- Sourcing and identifying potential suppliers
- Negotiating prices and terms with suppliers
- Creating and managing purchase orders
- Coordinating with logistics and transportation to ensure the timely delivery of goods
- Managing inventory levels and tracking purchase orders
- Maintaining relationships with suppliers
- Resolving issues related to the quality or delivery of goods
We are working closely with other departments such as production, logistics, and finance to ensure that the company’s purchasing needs are met in a timely and efficient manner.
KingsBox Logistical service – making sure the products are delivered on time, at the right location
KingsBox logistical service refers to the coordination and management of the movement of goods and materials. This includes the planning, implementation, and control of the efficient and cost-effective flow of materials, in-process inventory, and finished goods from the point of origin to the customer.
The main goal is to ensure that the right products are delivered to the right place, at the right time, and in the right quantity. This may involve a variety of tasks such as:
- Transporting goods from suppliers to warehouses or manufacturing plants
- Storing and managing inventory levels
- Planning and scheduling deliveries to customers
- Coordinating with transportation companies or 3rd party logistics providers
- Managing the return and disposal of goods
- Managing the flow of goods through the supply chain
- Managing the tracking and documentation of goods in transit
KingsBox has an effective logistical service, which is helping to increase efficiency, reduce costs, and improve customer satisfaction.
KingsBox warehouse – storing and preparing the equipment for the delivery
KingsBox warehouse is used to store and manage the materials, equipment, and finished products related to packaging operations. We are storing materials such as cardboard, plastic parts, steel parts and all purchased or produced equipment.
We are also storing finished products such as packaged goods, ready for distribution and delivery to customers. The KingsBox warehouse includes specific areas for packaging assembly, quality control, and inventory management.
We are having loading docks or other means for receiving and shipping materials and products, as well as materials handling equipment such as forklifts and pallet jacks to move materials around the facility.
In KingsBox warehouse modern technologies and automation is used to improve efficiency, accuracy, and traceability, such as barcodes and warehouse management software.
KingsBox and global supply chain during the pandemic
The COVID-19 pandemic has caused significant disruptions in the container shipping industry. Some of the main problems that have emerged include:
- Port Congestion: Many ports around the world have experienced severe congestion as a result of reduced capacity due to social distancing measures, increased demand for goods, and a shortage of available cargo containers. This has led to delays in loading and unloading ships and increased lead times for cargo.
- Equipment Shortages: The pandemic has led to a shortage of shipping containers, with many containers stranded at ports or being held at their origin by suppliers. This has created a bottleneck in the supply chain and increased costs for shippers.
The pandemic has caused widespread disruption to global supply chains, with many factories shutting down or operating at reduced capacity. This has resulted in a slowdown of production and an imbalance in the demand and supply of goods, leading to increased freight rates and difficulty in securing shipping space.
Many shipping lines have reduced the number of sailings to manage the impact of the pandemic, leading to reduced capacity and increased competition for shipping space.
Due to port congestion and equipment shortages, cargo is often held in ports or terminals for longer periods, resulting in increased demurrage and detention charges for shippers.
Shifting to LCL shipping mode during the pandemic.
LCL (Less than Container Load) shipping is a method of shipping where multiple small shipments from different customers are consolidated into a single container. This is in contrast to FCL (Full Container Load) shipping, where a single customer rents an entire container for their exclusive use.
Switching to LCL shipping had several benefits for a company, such as:
- Reduced costs: LCL shipping typically costs less than FCL shipping as the costs of the container and transportation are shared among multiple customers.
- Increased flexibility: LCL shipping allows companies to ship smaller quantities of goods, making it more suitable for businesses with lower volume or less frequent shipping needs.
- Access to new markets: LCL shipping can allow companies to access new markets that would otherwise be cost-prohibitive using FCL shipping.
However, there were also some potential downsides to LCL shipping to consider:
- Increased lead times: LCL shipments may take longer to reach their destination as the consolidation and deconsolidation of cargo at ports can add additional time.
- Increased risk of damage: LCL shipments may be at a higher risk of damage as the cargo is consolidated with other shipments and may be handled more frequently.
- Limited control over delivery schedule: With LCL shipping, companies may have less control over the delivery schedule as the shipping schedule is determined by the shipping line.
Overall, LCL shipping was a cost-effective and flexible option for businesses with lower volume or less frequent shipping needs, but it is important to weigh the pros and cons and understand the potential impacts on lead times, delivery schedules, and cargo handling before making the switch from FCL to LCL
Increasing collaborations with local and other EU suppliers
During pandemic this way of cooperation proved to be a good alternative for KingsBox, because of:
- Reduced Lead Times
Local suppliers were often able to deliver goods faster than suppliers located farther away, as they were closer to the company’s manufacturing or distribution facility. It was a help to reduce lead times and increase efficiency.
- Improved Communication
Working with local suppliers turned out to be easier to communicate and coordinate with them, which helped to reduce the risk of errors or misunderstandings. This also helped to improve the overall quality of the goods provided.
- Reduced Transportation Costs
Using local suppliers helped to reduce transportation costs, as the goods didn’t have to travel as far to reach the company’s facility. This helped to lower overall costs and increase profitability.
- Increased Support for the Local Economy
By using local suppliers, a company helped to support the local economy, which was beneficial for the community and the company’s reputation.
- Increased Responsiveness to Changes in Demand
Local suppliers are more responsive to changes in demand, as they are closer to the company and can make adjustments more quickly.
- Greater Control over Supply Chain
Greater control over its supply chain vas given using local suppliers, allowing us to monitor and manage the production process more closely.
- Greater Resilience to Disruptions
Using local suppliers helped to mitigate the impact of supply chain disruptions caused by factors such as natural disasters, the Evergreen vessel blocking all traffic in the Suez Canal, port closures, or pandemics, as they are less likely to be affected by these events.
It is important to note that, depending on the product in some cases is not possible to use only local suppliers. However, using them whenever possible provided many benefits for KingsBox and the local community.
Summary
As you can see, the supply chain is very interesting, active and diverse topic. It is one of our main priorities to improve in that area, as it is very important to produce and deliver quality equipment in time. Our team is facing different challenges daily, and always looking for ways to improve and negotiate, to make our customers happier and exceed their expectations.
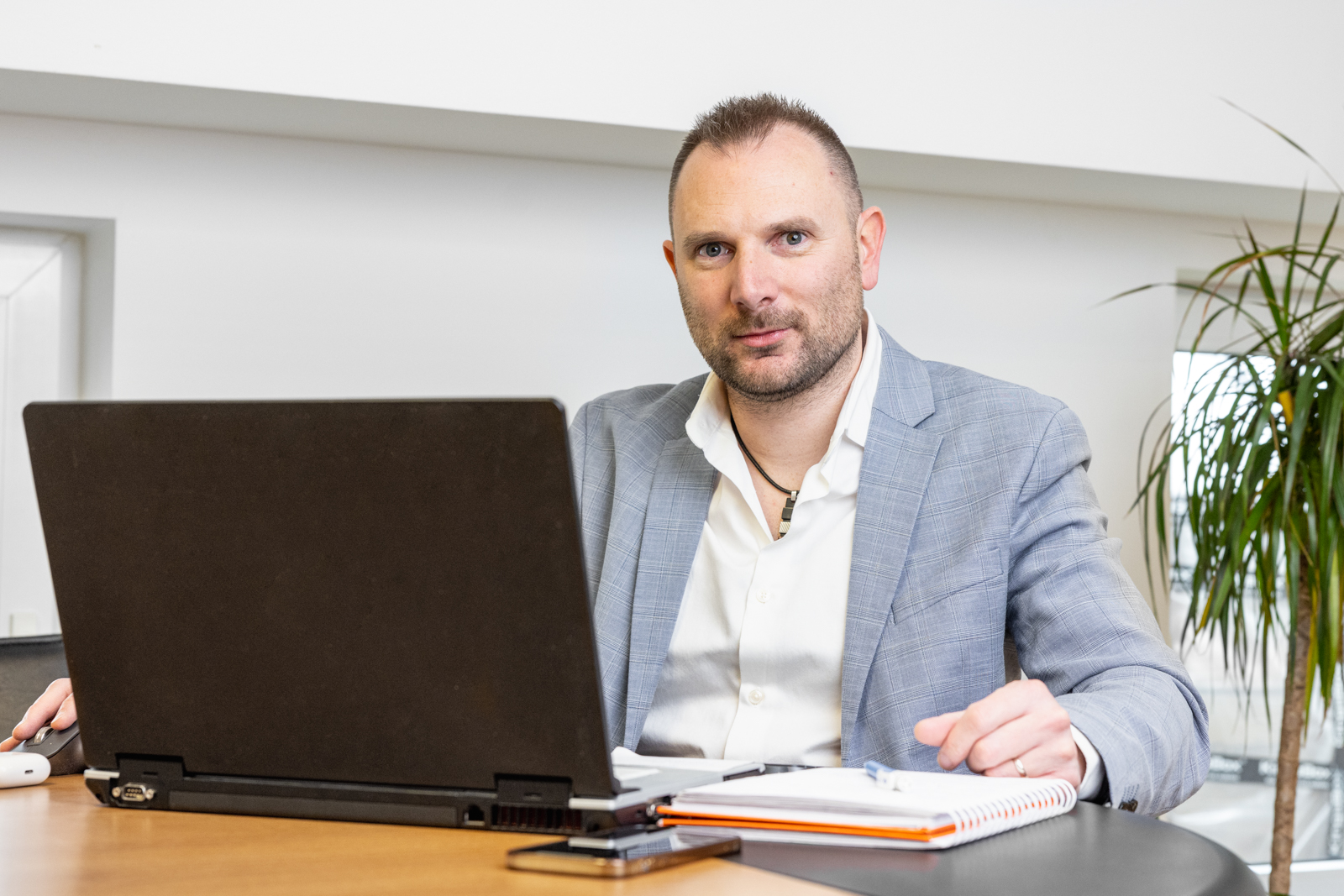
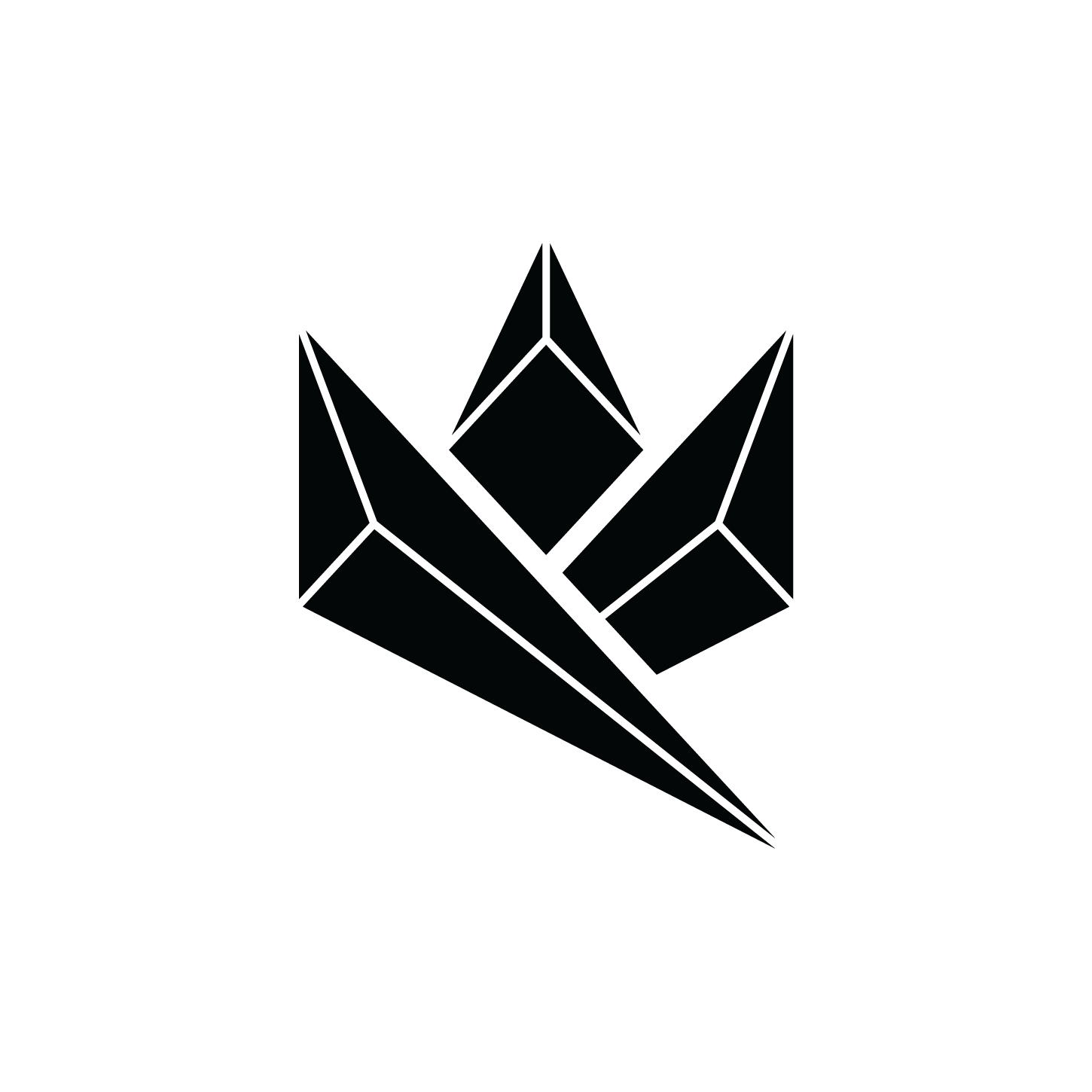